"Most of the metal components that we use every day, for instance, in an aircraft, automobile, surgery tools in hospitals, are heat treated."
Manufacturing
Nitrex
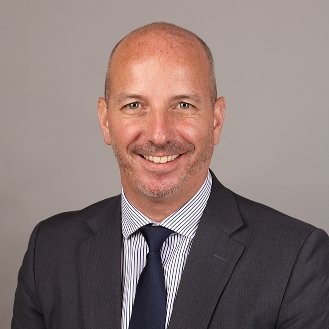
Innovative surface treatment solutions that make our world run better
Nitrex is helping manufacturers across the globe achieve greater tolerances, meet the highest standards, and become more profitable along the way
Nitrex
Innovative surface treatment solutions that make our world run better
Nitrex is helping manufacturers across the globe achieve greater tolerances, meet the highest standards, and become more profitable along the way
Nitrex
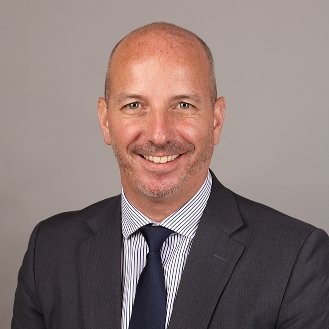
Even the toughest of materials wear down over time, and in a world that is trying to get more use out of available resources, looking after and maintaining the things that we have is a route to better efficiency and ultimately, a more sustainable future.
For nearly 40 years, Nitrex has been at the forefront of some of the most advanced surface treatment solutions that meet the increasingly stringent requirements for the industry. Considered experts in their field, the company is enabling manufacturers to push boundaries in production processes, cost efficiency, and sustainability.
Iwo Korwin, President of Global Nitrex Turnkey Solutions, gives an overview of what the company does:
“Nitrex was founded in 1984 in Montreal, Canada, as a company that wanted to develop a revolutionary new way of controlling the nitriding process called Nitreg®: a thermochemical process that hardens the surface of metallic components to extend their service life. We commissioned the first installation in 1987 and the company has grown rapidly ever since. Currently, the company has three business units: the equipment (turnkey systems) division, the software and instrumentation division, and the commercial heat treating division, the latter which provides heat treating services to companies that cannot or do not wish to do it in-house.”
Controlled nitriding does not transform the core hardness of components but enhances the surface hardness, making treated parts more durable and less vulnerable to wear, fatigue, and corrosion. As such, Nitrex is a global partner to many companies that manufacture components that are in use in homes, in the sky, on the road, in businesses and factories every day – helping companies bring more value and even better performance to manufactured parts while operating in a greener way.
Jean-Francois Cloutier, CEO at Nitrex says that the practical applications are limitless:
“Most of the metal components that we use every day, for instance, in an aircraft, automobile, surgery tools in hospitals, are heat treated. At Nitrex, we design and manufacture furnaces, as well as software, controls, and accessories you might think of that would go on to a furnace. Our solutions consistently set industry benchmarks and exceed the most stringent requirements for performance.”
The company structure has a robust quality control process built-in. The different business units effectively make Nitrex their own customer first: heat-treating products and solutions are tested rigorously by the business units in real-world environments before they are sold to external customers. Using this approach, Cloutier says that their markets – chiefly aerospace, automotive, industrial and renewable energy – can leverage proven solutions for greater reliability, predictability and speed:
“We usually serve blue-chip customers. That's a unique position in the market. Nitrex has the ability to precisely control the quality of production. From our library of over 4,000 proven formulae or recipes, we are able to pick a formula and customize it in our laboratory to the customer’s specific application and production needs.”
Such knowledge enables innovation to happen and makes customers achieve remarkable success. Nitrex is the first company to offer a fully automated nitriding/nitrocarburizing system, ultimately allowing engine manufacturers to produce lighter, more fuel efficient, and even less expensive engines. Jack Kalucki, Senior International Account Executive at Nitrex says that innovations such as these have revolutionized the entire industry:
“Nitrocarburizing was a low value-added heat-treating process. We came on board with the same control idea as for Nitreg® nitriding and derived Nitreg®-C for nitrocarburizing: a variation of the nitriding process whereby nitrogen and carbon simultaneously diffuse into the surface of the steel. Other innovations include the growth in nitriding of stainless steels. So, we came up with a process applied to stainless steels called Nitreg®-S. We also developed a low-temperature surface hardening process for stainless steels, mainly used for components where you need to avoid the formation of chromium nitrides/carbides and loss of corrosion properties. It's called Nano-STM.”
Kalucki explains the practical use of this technology:
“Extrusion dies are used for most of the extruded components we see in the world, where aluminum has been pushed through a steel die opening to produce a precise shape. The extrusion process will eventually wear out the die. These dies are extremely expensive so when we re-nitride the part, we actually prolong the life by 15 or 20 percent, which makes a huge impact on how cost-efficient extruders are and their bottom line.”
The willingness of Nitrex to support and partner with other businesses has led to long-term relationships that have benefited both sides. Steve Mueller, Associate Director for Business Development at Linde explains how their collaboration has added value to a third party:
“Linde and Nitrex had been working together for more than 10 years and counting. One of our customers who manufactures copper wire had an issue with a high scrap rate. We brought in Nitrex to help that customer specifically with furnace issues. We were able to install a completely new control system on the furnace and their scrap rate went down dramatically: within a few months, the savings paid for all the equipment that they had purchased.”
For Jean-Francois Cloutier, manufacturing is only going to continue to innovate and thrive – and he intends Nitrex to be at the heart of it:
“More customers are asking for smarter and more environmentally friendly solutions, which Nitrex has because the technology that we are using in our gas nitriding systems and vacuum heat-treating furnaces can respond to those challenges. The vision for the future is to help our customers build products that are stronger for longer than others dare to dream.”